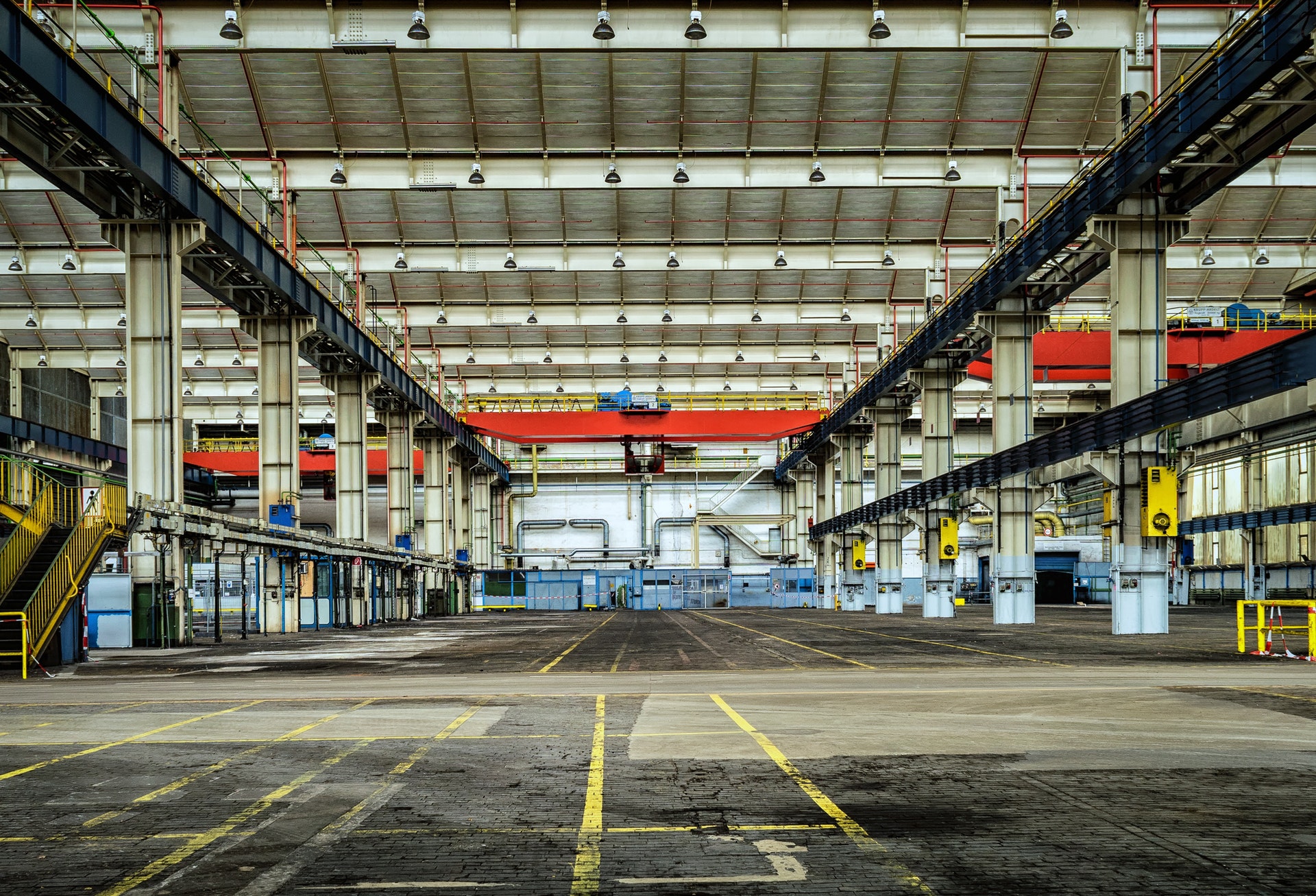
Plastic injection molding is a simple process where plastic pellets are placed into an injection unit, and the heating band around it will melt the plastic so that it turns into molten. The molten is then injected into a mold, which is made up of two halves that will draw back and release the plastic object that has already hardened.
There are many benefits that come with this method of plastic molding compared to other plastic molding processes.
Cost-effective
As a large plastic injection molding company, Pro-Fine Sdn Bhd possesses a range of automated machines such as the Kawaguchi KM280B3, Sumitomo SE50DU, Weltech F2V90 and more which is the foundation of this molding process. The molds and machines may have a high initial cost, but when production begins, companies are able to achieve a breakeven point very quickly.
Another advantage that comes with plastic injection molding machines is the redundancy of labour force. The whole manufacturing process requires very little or no supervision because the machines automatically perform injection molding, hence it only requires one person to manage and control the system. Post-production stage usually requires minimum labour as well due to a consistency in the machine-made products.
Reduced labour costs will in turn, lower the cost of products. Thus, consumers will be able to purchase these products at a lower cost.
High production output
A high efficiency in the production of plastic injection products is required to fulfil the demands of plastic injection molding in Malaysia and overseas. Correspondingly, the speed of the machines allows mass production, which satisfies the needs of local and international consumers.
Essentially, you need to set up the machine with specifically-designed injection molds and programme the presses before the process can begin. Molds can be highly priced, but with one mold, you are able to mass produce plastic components in large numbers. Additionally, these machines work at very high speeds, but it also depends on the number of impressions (part molds) that are in the tool. Some only have one part in a mold, while molds for bottle caps can reach up to 128. Generally, cycle times are between 15-30 seconds.
As a large plastic injection molding company in Malaysia, we have ample resources that are combined with an organised system in order to mass produce quickly. Thus, the costs of the products are low, enabling us to sell them at affordable prices to our customers.
Material & design flexibility
Injection molding is very flexible in terms of material and design. You can use different types of materials simultaneously in the production of plastic components. One example is the co-injection method, where two types of plastic are flowed through two different tubes, and injected into the mold together to form a molten mixture.
We have a wide range of plastic materials such as polypropylene (PP), polypropylene carbonate (PPC) and acrylonitrile butadiene styrene (ABS), to name a few. By mixing a few types of plastic materials, we are able to reduce costs, produce stronger plastic articles which can even replace steel in some situations.
On the other hand, customers can choose all types of designs for the plastic components that are to be manufactured. Intricate designs with complicated details are easily manufactured with the plastic injection molding method. Once the mold has been created, the upcoming process is straightforward as the machine will be able to function on its own. Due to its flexibility, Pro-Fine provides the option of custom plastic injection molding to our clients in spite of tricky and complex designs.
Additionally, our clients can customise the colour of their products. The high-quality colour pellets have a high fade resistance and the colours are long-lasting. The base for the process is the mold, hence we can change the colour of the part anytime as long as the mold is present.
Precision & consistency
Machines used for injection molding are very accurate. Injection molding forges small plastic parts that are very precise, reaching a measurement that is within 0.005 inches. Customers are free to customise all types of complex designs because of the precision that injection molding provides. What causes the details to be created almost perfectly is the pressure that injection molding offers. Although it also depends on the type of plastic used, these machines are conventionally producing an average low of 0.005 inches. The most important part is the mold, so if it is well-made, the whole process should be working smoothly and rapidly. Custom injection molding prohibits errors as well due to the presence of a mold that is properly made. Furthermore, injection molding products barely need to go through the post-production process because of its precision.
Injection molding is highly repeatable as well. This means that there is a consistency among products even though they are from different batches. The second batch will be identical to the plastic components of the first batch. Product consistency maintains your brand image because of the low defect rate and the uniformity in all of your products.
Reduced waste
Pro-Fine aims to conserve resources and energy while playing a part in recycling and preventing pollution. In line with Pro-Fine’s company policy, plastic injection molding carves a path for sustainability because of reduced waste. The high tolerance in injection molding produces little leftover or zero scraps during the process. Scrap loss amounts to zero under a stable production, ensuring that none of the materials are wasted.
When excess materials are present, they can be reused as most plastics are recyclable. The scraps will have to go through another cycle of grinding and melting if they are to be used again. Reground material is usually used for parts that are less important and do not require high performance properties. Additionally, companies can also reuse or recycle unused molding plastic. Overall, plastic injection molding does not only save resources, it helps to save the costs of companies too.
Pro-Fine is a Malaysian plastic molding manufacturing company that emphasises on its use of plastic injection molding while conserving the environment, meeting the current industrial standards and societal requirements.